Non-Consumable Electrode
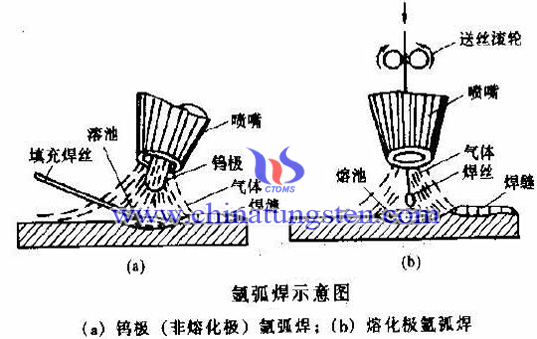
Introduction
Non-consumable electrode refers to rare earth tungsten electrode and tungsten electrodes, such as pure tungsten electrodes, thorium tungsten electrodes, cerium tungsten electrode, lanthanum tungsten electrode, yttrium tungsten electrode, composite electrode (Triad electrode). Non-MIG arc is that arc burn between non-consumable electrode (usually tungsten) and the workpiece, a inactive gas would flow around the welding arc which would not react with metal, and then it would form a protective hood, so that tungsten pole end, arc and weld pool and the metal which is already under a high temperature condition that would not contact with the air, preventing oxidation and the absorption of harmful gases. Thereby forming a compact welded joint whose mechanical performance is very good.
Comparison between Non-consumable Electrode and Consumable Electrode
Welding stick would be fed through the wire wheel, current contact nozzle would conduct electricity, arc would between the base metal and welding wire, and melting them. Difference between consumable electrode and TIG are: wire is used as the electrode for the former, and it is constantly filled in melt pool, forming weld joint; the other is the use of protective gas, with applications of TIG welding technology, protective gas has been developed from a single gas to mixture gas, such as Ar 80% + CO220% argon-rich shielding gas. The former is usually referred to MIG, the latter is known as MAG.
Welding Notice
Non-consumable electrode weld aluminum and aluminum alloy and its operating methods and precautions are as follows:
1) AC power supply, argon with 99.99% high purity argon. Impure argon or poor quality welding wire will lead welding layer become gray.
2) Check assembling of tungsten tip before welding, tungsten tip should be ground into a conical shape to facilitate concentrated arc, stable combustion. And outer elongation is generally 5MM, ensure tungsten tip should be at the center of welding tip which cannot be deflected.
3) Arc strike should adopt high-frequency ignition device, it would be better to burn arc on the arc plates, when it is stable and tungsten tip is heated after a certain temperature, arc will be transferred to the welding area.
4) The mutual position of the welding torch, welding wire and the workpiece should be benefit to operate and can well protect the molten pool. Angle of welding stick should be small, if the angle is too large, which is possible to disrupt the stable of arc and gas.
5) Usually adopt left welding method. During welding, the welding wire in argon protective layer continues to reciprocate (drip) into the molten pool, and the welding wire and tungsten electrode can maintain a certain distance, the wire should be melted in the bath. After the welding, surface would become clear and uniform herring-bone form. When welding the fillet or lap joint, wire is continuously fed uniformly to the pool, after welding, surface smooth without scaly.
6) If interrupt or end the welding, operators should pay more attention to prevent crater cracks and contraction cavities. For those weld assembly which cannot be installed run off tab, the welding current should gradually weaken at the end of welding, and then arc should be slowly moved away.
7) After breaking arc, do not stop argon immediately, operators should wait for five seconds to 10 seconds and then turn off it, to prevent oxidation of tungsten.